Table of Content
- Before You Start: Buying the Right Land
- Winter vs Summer Manufactured Homes Prices in the Western Region
- Comparing Prices. New Manufactured vs New Single-Family Site-Built Homes. Cost per Foot Square
- Cost To Move A Modular Home
- The following are some ways that you can save money on your prefab home construction:
Choose a design from tiny homes to mid-sized houses, and pre-cut materials are delivered to your building site. The signing-off of the finished materials is another reason why kit homes help save builders time and money. Prefab homes began flourishing during the 19th-century gold rush in California, and since then they’ve developed into the mobile home, tiny home, and modular home movements. If you're considering building a home instead of buying one, it's important to understand the upsides and downsides of prefab homes.

Fit in a living room, two bedrooms, and a small kitchen and bathroom, or create three large rooms for hobbies and work. If you’re considering building a new home, then modular homes could be exactly what you’re looking for. View our floor plans, or call us to talk to one of our professional housing consultants for more details on homes for sale near you. These homes can appreciate in value like site-built homes since they have lasting foundations, and the buyers also own the land. One of the benefits of prefabricated homes is that they are generally speaking more eco friendly than stick built homes. Wheelhaus offers luxurious prefabricated homes, which start at $82,000.
Before You Start: Buying the Right Land
Best of all, so long as site work is completed, it should take two experienced DIYers roughly four days to complete, according to the company. The Guest House comes in a variety of sizes, too, customizable based on your needs. There is the standard 12-by-16-foot option or the much larger 32-by-36-foot barn space. Even better, it is easy to build within a week or so, though if you have access to a crane it can make it all the easier to construct.
This 117-square-foot tiny home packs a wallop with practicality and a rustic, Old West aesthetic that can make it easy to take along on the road. Building a home has never been more difficult when going through traditional means. If anything, it has become more costly and time-consuming to get the home that you have been dreaming of.
Winter vs Summer Manufactured Homes Prices in the Western Region
Modular homes hold their resale value and last just as long as other properties. If the market is growing in your area and home prices are increasing, then your home’s value will likely increase along with it. As long as you care for your home and continue to invest in it, going the modular route can pay off.
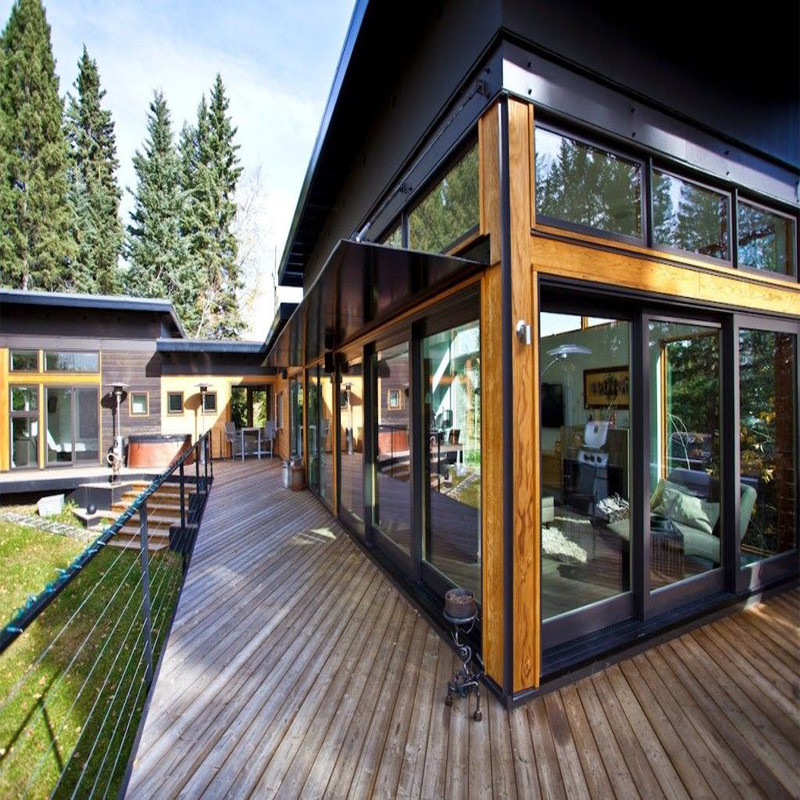
Some will argue that prefab homes are mass-produced by large companies in centralized factories. As these businesses do this for profit, they will not use the highest quality or expensive materials available. Most prefab companies are still using loose, batt insulation that is often falling out of the framing by the time the modules reach the site. Batt insulation alone is not what is making the better green homes out there more energy efficient. Nonetheless, after you pay for the delivery, transport insurance, and a crane to place it, the costs for the average custom home are approximately the same. Most studies concluded that there is no price difference in the actual construction from start to finish.
Comparing Prices. New Manufactured vs New Single-Family Site-Built Homes. Cost per Foot Square
The finished cost includes land preparation, the foundation, the permits, the utility connections, and other costs related to the house. A Manufactured Home is a home built entirely in the factory under a federal building code administered by the U.S. Manufactured homes may be single- or multi-section and are transported to your home site and installed.
LivingHomes offers three models of single family and multi-family homes that are all fully customizable. Also, rather than hiring individual contractors for different parts of the house such as roofers, electricians, etc., in modular homes all features are compiled in the factory. All of these features will need to be included in your price calculations to gauge an accurate price range for your new prefab home. On average, a prefab home costs between $90 and $120 per square foot. Also, remember that many prefab builders can take care of some of this work for you, particularly the process of securing building permits.
This makes them a widely-accepted form of new construction, not subject to the same zoning restrictions that frequently limit the placement of manufactured and mobile homes. In other words, prefab homes must meet the same building codes as traditional “sticks and bricks” construction, so you can build a prefab home practically anywhere. Essentially, prefab homes are homes that are constructed in a factory before being shipped to a building site in pieces, where they’re then assembled on-site in a matter of days. Unlike manufactured or mobile homes, which must meet the federal building code administered by the U.S. Department of Housing and Urban Development , prefab homes must be constructed according to state or local building codes. The high cost of building and buying a home, however, deters most people and locks them out of the real estate market.
DC Structures works with customers to create one-of-a-kind barn home kit designs that reflect each homeowner’s unique vision. These kits create permanent homes rather than mobile ones that you can easily transport to a new section of land. Although their price point is closer to that of a mobile home, customers can choose a design they love and easily create their permanent dream home. If you’re trying to stay within a tight budget, a kit home could be the answer you are looking for when building your new home. An average design plan to complete can cost you as little as $50,000 or as high as $350,000. Also known as prefab or modular homes, a kit home uses pre-cut pieces of wood to make building a new home both faster and cheaper.
You will not have to pay for inspectors coming out multiple times to check on your progress, nor will you have to pay high fees for getting all necessary licenses or permits approved. All these savings are passed on directly to you, allowing you to enjoy lower costs without compromising on quality or safety standards. The average cost for a 2 bedroom modular home is around $90 per square foot. You can get that number down even lower by looking at smaller modular homes or larger ones .
Build times from the point of order to move-in take roughly three to four months. Don’t let the term “prefab home” scare you away — today’s prefabricated homes (also termed “building systems” by the National Association of Home Builders), are downright fabulous. A modular home is a house that is made in a factory and then transported to the building site. The pieces of the house are assembled at the site, so it can be built quickly, cheaply and with less waste than traditional building methods. The cost of building a home is one of the biggest factors in determining whether or not you will be able to afford your dream house.
No comments:
Post a Comment